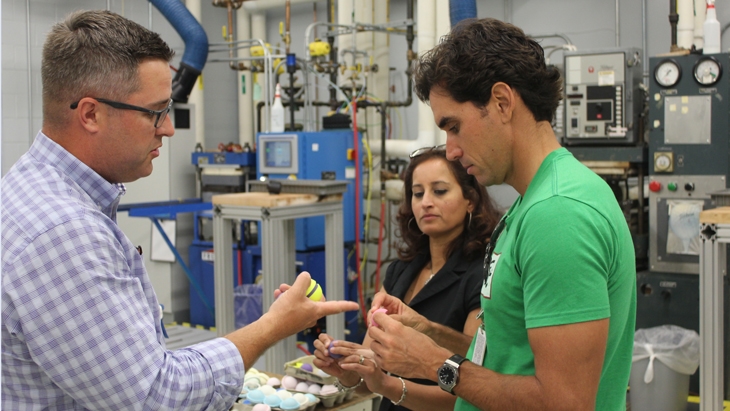
One by one, one second after another, Titleist Pro V1 golf balls drop out of a metal chute, filling a large plastic bin. The sound is soft and rhythmic. Watching this, Titleist Brand Ambassador Rafa Cabrera Bello is transfixed.
It's a few days before Labor Day weekend, just weeks from his debut as a member of the European Ryder Cup team. Rafa has spent the last five hours touring Titleist golf ball R&D and Operations facilities, watching firsthand how Titleist golf balls are designed, tested and manufactured. It’s been a long day – Rafa also spent three early morning hours at Rhode Island Country Club for a commercial shoot – yet, as 5 o’clock approaches here at Titleist Ball Plant 3 in southeastern Massachusetts, his eyes remain wide open, watching brand new Pro V1 golf balls pile up – almost literally hot off the press.
The metal chute is attached to an X-ray machine. Rafa’s tour guide, Kevin Ribeiro, a Team Leader in the Core Mixing division, points to an adjacent computer screen. It flickers with X-ray after X-ray, scanning the constructions of each ball.
“Have you heard the story,” Kevin asks, “about how Titleist started?” Rafa shakes his head.
That story, if you haven’t heard it, is about a serious golfer named Phil Young who missed a well-stroked putt on the final hole of match at New Bedford Country Club (not even a 15 minute drive from Ball Plant 3). Suspicious of his golf ball’s inconsistent performance, Young asked his playing partner, head of the X-ray department at a nearby hospital, to X-ray the ball. Sure enough, the core was off-center.
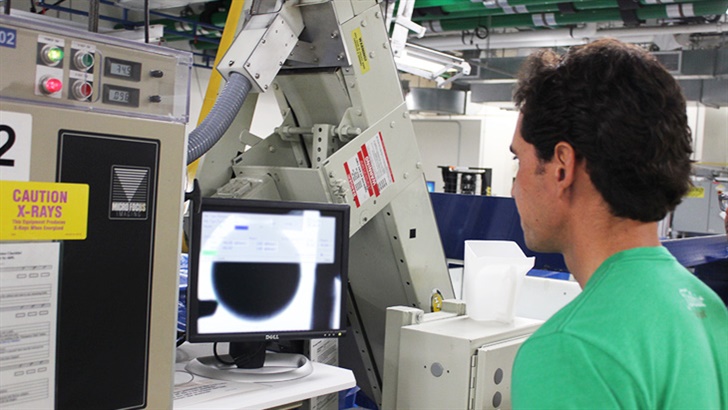
“What year was that?” Rafa asks.
“1932.” Three years later, Young, with the help of MIT classmate Fred Bommer, introduced the first Titleist golf ball, which was quickly embraced by golfers as the best performing, highest quality and most consistent golf ball ever made. Applying a lesson well learned, Young implemented a critical process check that still exists today: X-rays. Every new Pro V1 and Pro V1x golf ball is X-rayed. It’s the final step of a rigorous manufacturing process that totals more than 100 product and process quality checks.
Rafa smiles and nods. He exits the manufacturing floor, stepping through a door and into the front lobby. “I knew it was complicated, but a car plant is not that much more sophisticated,” he says.
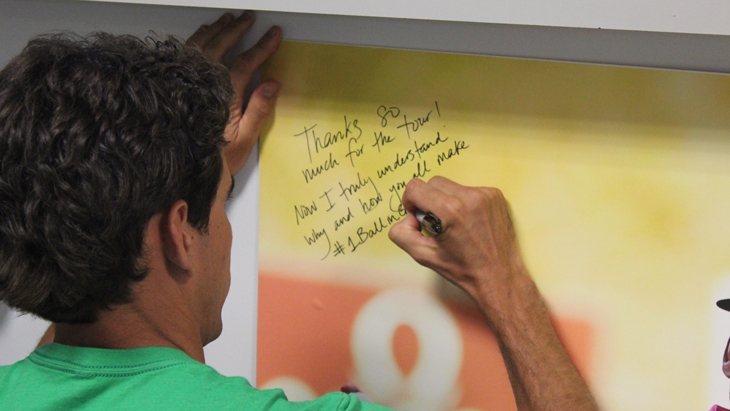
Before leaving the building, Rafa is asked to sign a poster-sized image of himself to commemorate the visit. Sharpie in hand, he writes:
“Thanks so much for the tour! Now I truly understand why and how you all make the #1 ball in golf!”
Just outside the front door, a group of about seven ball plant associates are eating together during their break. Rafa’s about four steps from his car when one of them yells, “Thank you for playing our ball!”
A bit startled, but now smiling, Rafa looks back and waves. “Thank you! It’s a really good ball!”
Here a few other fun facts we learned from Rafa:
• Rafa has been playing Titleist ever since he was “about 12 years old,” he said. “I think Tour Balata was my first ball.”
• Rafa marks his Pro V1x with his initials “RCB” written directly above the Titleist script on both sides. He’s been doing it that way for at least 10 years.
• Rafa doesn’t have any superstitions when it comes to play numbers. At the beginning of every tournament, he mixes up his dozen of #1s, #2s, #3s and #4s and plays whichever one he pulls out of the bag.
• Trajectory is very important to Rafa. Whenever he tests a new ball, he’s mostly focused on whether or not it fits in his “window” on different types of shots.
• Rafa loves to get technical! His scheduled one-hour visit to Golf Ball R&D ended up taking more than two hours because of all the questions he had for his tour guides, R&D associates Scott Cooper and Manjari Kuntimaddi. “I could have stayed there all day,” he said.
Check out the slideshow below for a look at Rafa’s day behind-the-scenes at Titleist Golf Ball R&D and Ball Plant 3.
_________________________________________
- Eric Soderstrom, Manager of Communications